Commercial PV
Units using capacity above represent kWDC.
2021 ATB data for commercial solar photovoltaics (PV) are shown above. The Base Year estimates rely on modeled capital expenditures (CAPEX) and operation and maintenance (O&M) cost estimates benchmarked with industry and historical data. Capacity factor is estimated based on hours of sunlight at latitude for five representative locations in the United States. The 2021 ATB presents capacity factor estimates that encompass a range associated with advanced, moderate, and conservative technology innovation scenarios across the United States. Future year projections are derived from bottom-up benchmarking of PV CAPEX and bottom-up engineering analysis of O&M costs.
The three scenarios for technology innovation are:
- Conservative Technology Innovation Scenario (Conservative Scenario): lower levels of R&D investment with minimal technology advancement and current global module pricing
- Moderate Technology Innovation Scenario (Moderate Scenario): R&D investment continuing at similar levels as today, with no substantial innovations or new technologies introduced to the market
- Advanced Technology Innovation Scenario (Advanced Scenario): an increase in R&D spending that generates substantial innovation, allowing historical rates of development to continue.
Resource Categorization
The ATB provides the average capacity factor for 10 resource categories in the United States, binned by mean GHI. Average capacity factors are calculated using county-level capacity factor averages from the Renewable Energy Potential (reV) model for 1998–2019 (inclusive) of the National Solar Radiation Database (NSRDB). The NSRDB provides modeled spatiotemporal solar irradiance resource data at 4-km spatial and 0.5-hour temporal resolution. The county-level mean GHI is calculated by aggregating each individual NSRDB point’s multiyear mean GHI to provide a county’s mean GHI for all years included in the analysis. The U.S. average capacity factor for each resource category is weighted by the land area (square miles) of each county within the GHI resource category. The county estimated land area is provided by geospatial and tabular data from the U.S. Census.
The map below shows average annual GHI in the United States.
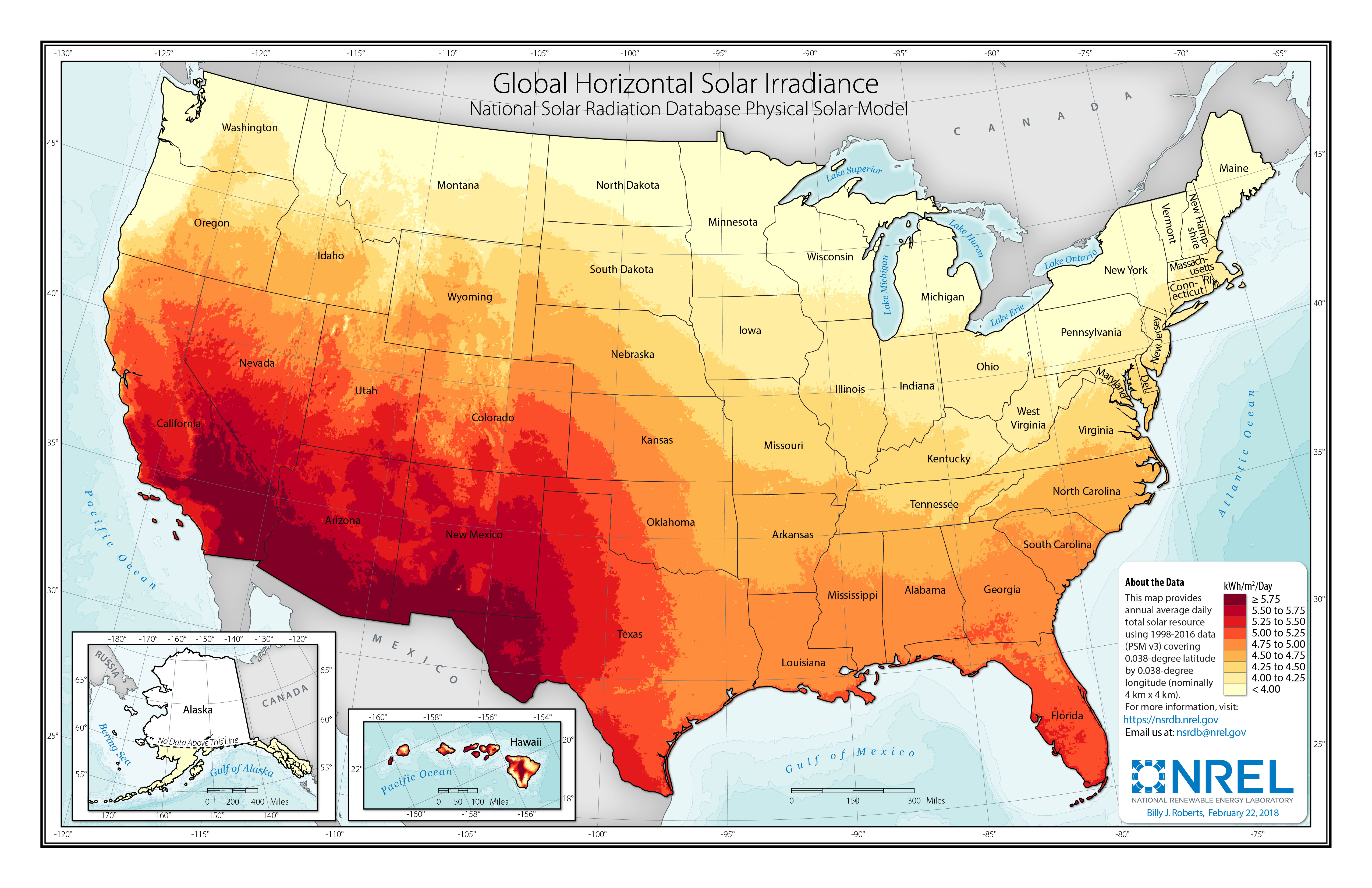
The following table summarizes the estimated 2019 (Base Year) year 1 capacity factors per resource category and each resource category's associated population.
Resource Class | GHI Bin | Mean DC Capacity Factor | Population |
---|---|---|---|
1 | >5.75 | 19.8% | 12,554,678 |
2 | 5.5–5.75 | 19.1% | 21,403,290 |
3 | 5.25–5.5 | 18.0% | 13,476,871 |
4 | 5–5.25 | 17.1% | 30,603,630 |
5 | 4.75–5 | 16.3% | 45,176,116 |
6 | 4.5–4.75 | 16.1% | 39,880,837 |
7 | 4.25–4.5 | 15.3% | 31,742,606 |
8 | 4–4.25 | 14.6% | 80,155,804 |
9 | 3.75–4 | 14.0% | 40,755,023 |
10 | <3.75 | 12.7% | 10,255,830 |
U.S. Mean | 15.8% |
DOE’s Solar Energy Technologies Office sets its PV cost targets for a location centered geographically within the continental U.S., in resource class 7, whereas the ATB benchmark is class 5, representing the national-average solar resource.
Scenario Descriptions
Scenario | Module Efficiency1 | Inverter and Power Electronics | Installation Efficiencies | Energy Yield Gain1 |
---|---|---|---|---|
Conservative Scenario | Technology Description: Tariffs expire, as scheduled, though some form of friction still remains, keeping U.S. panel pricing halfway between current U.S. and global pricing. Efficiency gains for panels are consistent with one standard deviation below that of the International Technology Roadmap for Photovoltaic (ITRPV—an annual document prepared by many leading international poly-Si producers, wafer suppliers, c-Si solar cell manufacturers, module manufacturers, PV equipment suppliers, and production material providers, as well as PV research institutes and consultants) to 2030—well below the historical monofacial average gains and below the leveling off point (21.5%) -$0.32/WDC Justification: This scenario represents the low end of manufacturers' expectations and additional friction despite the scheduled removal of the tariffs. | Technology Description: This scenarios assumes a larger market size. Justification: The global PV industry is expected to continue to expand. | N/A | N/A |
Moderate Scenario | Technology Description: Tariffs expire, as scheduled, and efficiency gains are consistent with median ITRPV road map to 2030, which is well below historical monofacial average gains and below the leveling off point (22.5%) -$0.19/W Justification: This scenario represents manufacturers' expectations for 2030. | Technology Description: This scenario assumes design simplification and manufacturing automation. Justification: Industry is currently switching to this practice. | Technology Description: This scenario assumes 30% labor and hardware balance-of-system (BOS) cost improvements through automation, preassembly of racking, mounting, and wiring efficiencies, and improvements in wind load design. Justification: This scenario represents lower levels of improvement than the historical average (Feldman et al., 2021). With increased global deployment and a more efficient supply chain, preassembly of mounting, racking, and wiring is possible. Best practices for permitting interconnection and PV installation (e.g. subdivision regulations, new construction guidelines, and design requirements) are being developed. | Technology Description: This scenario assumes a 10% energy gain through lower system losses, increased use of bifacial modules, improvements in bifaciality, and a degradation rate reduction from 0.7%/yr to 0.5%/yr Justification: Significant R&D is currently spent on improved cell temperatures and lower degradation rates. Companies will likely continue to focus on improved uptime to maximize profitability, and bifacial modules are already becoming a significant part of the global and U.S. supply chain. ITRPV estimates bifacial modules' world market share will grow from 10% in 2018 to over 60% by 2030. Industry participants have already demonstrated bifacial energy gains of 5%–33%, depending on the module mounting. |
Advanced Scenario | Technology Description: This scenario assumes modules maintain the historical average of 0.5% improvement per year (25%) -$0.17/W Justification: Manufacturers reported mass produced cell efficiencies will increase from 20%–23% in 2018 to 21%–24% by 2021. Mass production-monocrystalline and silicon heterojunction have already achieved cell efficiency records in a laboratory of 26.1% and 26.7% respectively.
| Technology Description: This scenario assumes design simplification and manufacturing automation Justification: The power electronics industry already has road maps to simplify and automate current products and there is more potential with increased industry size. | Technology Description: This scenario assumes 40% labor and hardware BOS cost improvements through automation and preassembly of racking, mounting and wiring efficiencies; the use of carbon fiber, which becomes low-cost, cuts mounting costs. Justification: This scenario represents lower levels of improvement than historical average (Feldman et al., 2021). With increased global deployment and a more efficient supply chain, preassembly of racking, mounting and wiring is possible. Reduction of supply chain margins (e.g., profit and overhead charged by suppliers, manufacturers, distributors, and retailers), will likely occur naturally as the U.S. PV industry grows and matures. Additionally, streamlining of installation practices through improved workforce development and training and developing standardized PV hardware is assumed. | Technology Description: This scenario assumes a 15% energy gain through lower system losses; increased use of bifacial modules, improvements in bifaciality and albedo enhancement to 0.3 (a white roof has an albedo of 0.7, there is likely to be suboptimal spacing, due to tight row spacing, which will cause shade); and a degradation rate reduction from 0.7%/yr to 0.2%/yr. Justification: In addition to the justifications listed above, industry participants have already demonstrated bifacial energy gains of 5%–33%, depending on the module mounting. |
Impacts |
|
|
|
|
References |
1 Module efficiency improvements represent an increase in energy production over the same area of space, in this case the dimensions of a PV module. Energy yield gain represents an improvement in capacity factor, relative to the rated capacity of a PV systems. In the case of bifacial modules, the increase in energy production between two modules with the same dimensions does not currently change the capacity rating of the module under standard test conditions, as the rating is based on light from one direction. Additionally, the rated capacity of a system does not increase with fewer system losses (e.g., panel cleanings).
Representative Technology
For the 2021 ATB, commercial PV systems are modeled for a 200-kWDC, fixed-tilt, roof-mounted system. Flat-plate PV can utilize direct and indirect insolation, so PV modules need not directly face and track incident radiation. This gives PV systems a broad geographical application, especially for commercial PV systems.
Distributed-scale PV is assumed to be configured as a fixed-tilt, roof-mounted system. Compared to utility-scale PV, this reduces both the potential capacity factor and land (roof) space that is available for development. A recent study of rooftop PV technical potential (Gagnon et al., 2016) estimated as much as 731 GW (926 TWh/yr) of potential exists for small buildings (< 5,000 m2 footprint) and 386 GW (506 TWh/yr) exists for medium (5,000–25,000 m2) and large buildings (> 25,000 m2).
Methodology
This section describes the methodology to develop assumptions for CAPEX, O&M, and capacity factor. For standardized assumptions, see labor cost, regional cost variation, materials cost index, scale of industry, policies and regulations, and inflation.
Currently, CAPEX—not LCOE—is the most common metric for PV cost. Because of different assumptions in long-term incentives, system location and production characteristics, and cost of capital, LCOE can be confusing and often incomparable for different estimates. Though CAPEX also has many assumptions and interpretations, it involves fewer variables to manage. Therefore, PV projections in the 2021 ATB are driven entirely by plant and operational cost improvements.
The Base Year estimates rely on modeled CAPEX and O&M estimates benchmarked with industry and historical data. Capacity factor is estimated based on hours of sunlight at latitude for 10 resource categories in the United States, binned by mean global horizontal irradiance (GHI).
Future year projections are derived from bottom-up benchmarking of PV CAPEX and bottom-up engineering analysis of O&M costs. Three projections are developed for scenario modeling as bounding levels:
- Conservative Scenario: lower levels of R&D investment with minimal technology advancement and current global module pricing
- Moderate Scenario: assume R&D investment continuing at similar levels as today, with no substantial innovations or new technologies introduced to the market
- Advanced Scenario: an increase in R&D spending that generates substantial innovation, allowing historical rates of development to continue.
Capital Expenditures (CAPEX)
Definition: Capital expenditures (CAPEX) are expenditures required to achieve commercial operation in a given year. For commercial PV, this is modeled for only a host-owned business model with access to debt.
For the 2021 ATB—and based on data (EIA, 2016) and the NREL Solar-PV Cost Model (Feldman et al., 2021) (Barbose et al., 2019)—the distributed solar PV plant envelope is defined to include items noted in the table above.
Base Year: In the chart below, reported historical commercial-scale PV installation CAPEX (Barbose et al., 2020) is shown in box-and-whiskers format for comparison to historical commercial-scale PV benchmark overnight capital cost and ATB future CAPEX projections. The data in (Barbose et al., 2020) represent 82% of all U.S. residential PV and commercial PV capacity installed through 2019.
Historical Sources: (Barbose et al., 2020); (Feldman et al., 2021)
Future Projections: 2021 ATB
All prices quoted in WAC are converted to WDC (1 WAC = ILR × WDC).
The difference in each year's price between the market and benchmark data reflects differences in methodologies. Reported and benchmark prices can differ for a variety of reasons, as outlined by Barbose and Darghouth (Barbose et al., 2019) and Bolinger, Seel, and Robson (Bolinger et al., 2019), including:
- Timing-related issues: For instance, the time between contract completion and project placement in service may vary.
- Variations over time in the size, technology, installer margin, and design of systems installed in a given year
- Which cost categories are included in CAPEX (e.g., financing costs and initial O&M expenses).
Federal investment tax credits provide an incentive to include costs in the upfront CAPEX to receive a higher tax credit, and these included costs may have otherwise been reported as operating costs. The bottom-up benchmarks are more reflective of an overnight capital cost, which is in-line with the ATB methodology of inputting overnight capital cost and calculating construction financing to derive CAPEX.
Commercial PV pricing and capacities are quoted in kWDC (i.e., module rated capacity) unlike other generation technologies (including utility-scale PV), which are quoted in kWAC. For commercial PV, this would correspond to the combined rated capacity of all inverters. This is because kWDC is the unit that the majority of the PV industry uses. Although costs are reported in kWDC, the total CAPEX includes the cost of the inverter, which has a capacity measured in kWAC.
CAPEX estimates for 2020 reflect continued rapid decline in pricing supported by analysis of recent system pricing for projects that became operational in 2020 (Feldman et al., 2021).
The historical chart above shows the range in historical CAPEX that reflects the heterogeneous composition of the commercial PV market in the United States.
The chart also includes a representative commercial-scale PV installation. Although commercial PV systems vary dramatically in size and application, typical installation costs are represented with a single estimate per innovations scenario. Additionally, commercial PV CAPEX does not correlate well with solar resource.
Although the technology market share may shift over time with new developments, the typical installation cost is represented with the projections above.
System prices of $1.76/WDC in 2019 and $1.72/WDC in 2020 are based on bottom-up benchmark analysis reported in U.S. Solar Photovoltaic System Cost Benchmark Q1 2020 (Feldman et al., 2021), adjusted for inflation. The 2019 and 2020 bottom-up benchmarks are reflective of an overnight capital cost, which is in-line with the ATB methodology of inputting overnight capital cost and calculating construction financing to derive CAPEX.
The Base Year CAPEX estimates should tend toward the low end of observed cost because no regional impacts are included. These effects are represented in the historical market data.
Future Years: Projections of 2030 commercial PV plant CAPEX are based on bottom-up cost modeling, with a straight-line change in price in the intermediate years between 2020 and 2030. The system design and price changes made in the models are summarized and described in the Summary of Technology Innovations by Scenario table. See below for the details of changes to components of system price in the different ATB scenarios.
We assume each scenario's 2050 CAPEX is the equivalent of the 2030 CAPEX of the scenario but one degree more aggressive, with a straight-line change in price in the intermediate years between 2030 and 2050. Asterisks indicate corresponding cells, where scenarios use the same values but shifted in time. We also develop and model a scenario one degree more aggressive than the Advanced Scenario to estimate its 2050 CAPEX. The 2050 Advances Scenario assumes a module efficiency of 30%, achieved through double-junction cells (perovskite on top of c-Si); further inverter simplification and manufacturing automation; 50% labor and hardware BOS cost improvements through automation and preassembly of racking, mounting, and wiring efficiencies; and that carbon fiber becomes low cost, replacing steel and aluminum and cutting material costs in half.
Year | Advanced (Increased R&D) | Moderate (Current R&D) | Conservative (Decreased R&D) |
---|---|---|---|
2030 | *Commercial PV CAPEX: $0.68/WDC | † Commercial PV CAPEX: $0.89/WDC | Commercial PV CAPEX: $1.43/WDC |
2050 | $0.51/WDC | *$0.68/WDC | † $0.89/WDC |
More aggressive scenarios reach given CAPEX sooner, as indicated by the asterisks and daggers
We compare the CAPEX scenarios over time to four analysts' projections, adjusted for inflation (see chart below). The 2021 ATB CAPEX projections are fairly in-line with other analysts' projections through 2030, with the exception of the analysts' maximum projection, which starts at a much higher CAPEX. Two of the four analyst projections do not go beyond 2030, so data points to compare the ATB projections are limited; however, the Advanced Scenario is in-line with the minimum analyst projection.
Source for CAPEX: NREL 2021; (BNEF, 2019); (BNEF, 2020); (Cox, 2020); (EIA, 2021)
All prices quoted in WAC are converted to WDC (1 WAC = ILR × WDC).
Use the following table to view the components of CAPEX.
Operation and Maintenance (O&M) Costs
Definition: Operation and maintenance (O&M) costs represent the annual expenditures required to operate and maintain a solar PV plant over its lifetime, including items noted in the table above.
Base Year: The initial figure on this page shows the Base Year estimate and future year projections for fixed O&M (FOM) costs. Three technology innovation scenarios are represented. The estimate for a given year represents annual average FOM costs expected over the technical lifetime of a new plant that reaches commercial operation in that year.
FOM of $19/kWDC-yr is based on modeled pricing for a commercial PV system quoted in 2019 as reported by (Feldman et al., 2021). The values in the 2021 ATB are higher than those from the 2020 ATB because we include costs in the 2021 ATB not previously calculated. These include four additional line measures (property taxes, insurance, asset management, and security) that are added based on feedback collected by Lawrence Berkeley National Laboratory (LBNL from U.S. solar industry professionals (Wiser et al., 2020). A wide range in reported prices exists in the market that depends in part on the maintenance practices that exist for a particular system. These cost categories include asset management (including compliance and reporting for incentive payments), insurance products, site security, cleaning, vegetation removal, and component failure. Not all these practices are performed for each system; additionally, some factors depend on the quality of the parts and construction. NREL analysts estimate O&M costs can range from $0 to $40/kWDC-yr.
Future Year: FOM of $19/kWDC-yr for 2020 is also based on pricing reported by (Feldman et al., 2021), which can be divided into system-related expenses ($15/kWDC-yr) and administration-related expenses ($4/kWDC-yr). From 2021 to 2050, system-related FOM is based on the historical average ratio of O&M costs ($/kW-yr) to CAPEX costs ($/kW), 0.8:100, as reported by (Feldman et al., 2021). Historical data suggest O&M and CAPEX cost reductions are correlated; from 2010 to 2020, benchmark commercial PV O&M and CAPEX costs fell 46% and 69% respectively, as reported by (Feldman et al., 2021). Administrative expenses are kept constant.
Use the following table to view the components of O&M.
Capacity Factor
Definition: Commercial PV system capacity factor is not directly comparable to other technologies' capacity factors. Other technologies' capacity factors (including utility-scale PV) are represented exclusively in AC units (see Solar PV AC-DC Translation). However, because commercial PV pricing in the 2020 ATB is represented in $/WDC, commercial PV system capacity is a DC rating. Because each technology uses consistent capacity ratings, the LCOEs are comparable.
The capacity factor is influenced by the hourly solar profile, technology (e.g., thin-film or crystalline silicon), the bifaciality of the module, shading, expected downtime, and inverter losses to transform from DC to AC power. The DC-to-AC ratio is a design choice that influences the capacity factor. PV plant capacity factor incorporates an assumed degradation rate of 0.7%/yr in the annual average calculation. R&D could increase energy yield through bifaciality, increased albedo, better soil removal, improved cell temperature, lower system losses, O&M practices that improve uptime, and lower degradation rates of PV plant capacity factor; future projections assume energy yield gains of 0%–31% depending on the location and scenario.
Base Year: In the interactive data chart at the top of this page, select Technology Detail = All to add filters to the initial figure on this page to show a range of capacity factors based on variation in solar resource in the contiguous United States. The range of the Base Year estimates illustrate the effect of locating a commercial PV plant in places with lower or higher solar irradiance. The ATB provides the average capacity factor for 10 resource categories in the United States, binned by mean GHI. The ATB provides the average capacity factor for 10 resource categories in the United States, binned by mean GHI. The annual average capacity factor for the contiguous United States is calculated using the Renewable Energy Potential (ReV) model using solar resource data for 2012 from the National Solar Radiation Database (NSRDB). The county-level capacity factors are calculated for specific locations with azimuth and tilt, which are based on representative agents selected in the Distributed Generation Market Demand Model (dGen) 2020 Standard Scenarios agent database (Sigrin et al., 2016). A lookup table for these locations and the National Solar Radiation Database (NSRDB) is generated based on nearest distance. The azimuth and tilt as well as the resource GID are used to generate a System Advisor Model (SAM) config file and to run ReV, which outputs the annual average capacity factor at each evaluated location. The U.S. average capacity factor for each resource category is weighted by the population of each county within the GHI resource category. The county estimated populations are provided by geospatial and tabular data from the U.S. Census.
Because of the change in methodology in calculating capacity factors in the 2021 ATB, they are not directly comparable to previous editions of the ATB. In the 2021 ATB, first-year operation capacity factors as modeled range from 12.7% for Class 10 (for locations with an average annual GHI less than 3.75) to 19.8% for Class 1 (for locations with an average annual GHI greater than 5.75).
Over time, PV installation output is reduced because of degradation in module quality, which is accounted for in ATB estimates of capacity factor over the 30-year lifetime of the plant. The adjusted average capacity factor values in the 2019 ATB Base Year range from 12.0% for Class 10 (for locations with an average annual GHI less than 3.75) to 18.6% for Class 1 (for locations with an average annual GHI greater than 5.75).
Future Years: Projections of capacity factors for plants installed in future years increase over time because of an increase in energy yield from the module (better tracking, improved cell temperature, bifaciality, and improved albedo), reduced system losses (improved soil removal, improved O&M uptime, and more-efficient inverters) and a reduction in degradation rates. The table below summarizes the technology improvements we used to calculate indicative improvements in capacity factor in each scenario.
Performance Area | 2019 | 2030 Conservative | 2030 Moderate | 2030 Advanced |
Bifaciality | none | None | 0.85 | 0.85 |
Albedo | 0.2 | 0.2 | 0.3 | 0.3 |
AC & DC losses | 14.3% | 14.3% | 10.4% | 7.5% |
Annual degradation rate | 0.7% | 0.7% | 0.5% | 0.2% |
The technology improvements summarized above would not necessarily result in the estimated capacity factor improvements, given the 2021 ATB assumption of a constant ILR. PV system ILR choice is based on an optimization exercise to maximize profits (or offer the lowest energy price), trading off the extra cost and increased clipping losses of additional modules, with improvements in inverter operation and a higher, flatter electricity production curve. All things being equal, the optimal ILR of PV systems in higher resource classes or those which use bifacial modules will be lower than the optimal ILR of systems in lower resource classes or those with monofacial modules, particularly without the use of storage. Because of the complexity of optimizing CAPEX and ILR for each resource class for each year, and with and without storage, ATB PV system CAPEX and capacity factor benchmarks are calculated using a fixed ILR, independent of system location, performance improvements over time, or the incorporation of storage. Additionally, we assume performance improvements over time are not location-dependent, despite the fact that a PV system with the same ILR in a higher resource area will experience more clipping, and thus lower performance improvements. However, in reality, PV systems in those areas would reduce their clipping losses by installing fewer PV panels and would thus have a lower upfront cost (trading off the marginally greater production with reduced CAPEX).
The following table summarizes the difference in average capacity factor in 2030 caused by these changes in the technology innovation scenarios. Similar to our CAPEX assumptions, we assume each scenario's 2050 capacity factor is the equivalent of the 2030 capacity factor of the scenario but one degree more aggressive, with a straight-line change in price in the intermediate years between 2030 and 2050. The table below summarizes capacity factors for each ATB scenario by resource class.
Scenario | Average Capacity (Class 10 - Class 1) | Percentage Improvement from 2019 |
---|---|---|
Advanced Scenario | 14.4%–22.3% | 20.0% |
Moderate Scenario | 13.4%–20.8% | 11.9% |
Conservative Scenario | 12.0%–18.6% | 0% |
We also develop and model a scenario one degree more aggressive than the Advanced Scenario to estimate its 2050 capacity factor. The 2050 Advanced Scenario assumes a 25% improvement over 2019 capacity factors.
References
The following references are specific to this page; for all references in this ATB, see References.